WHAT IS THE PAPER IMPREGNATION PROCESSES?
Paper impregnation processes are known as low pressure lamination.
Generally, wooden panels are covered with printed or colored hard paper for attractive and durable surfaces on furniture and floors. These types of decor papers are impregnated with melamine or urea resin in specially designed processors.
Usually these types of chemicals are covered in 2 parts:
The first is the chemicals that saturate all the building blocks of the paper with urea or melamine resin.
The other is chemicals that coat the paper surface with pure melamine resin.
These chemicals are used in application units and many drying ovens.
In these processes, the desired resin is to be spread uniformly on the building blocks of the paper and on the surface.
High quality paper impregnation is possible by choosing the right resin and additive chemicals.
High quality paper impregnation is possible with the most accurate adjustment of the viscosity and spreading rate of the resin and the selection of the right resin and additive chemicals. . In particular, latent catalysts and hardeners are designed to adjust this resin reactivity.
It is mandatory to use special purpose wetting agents (wetting agent LUFTCHEM SPEED R25) to achieve bright and homogeneous penetration and surface coating.
Also, another important issue is to be able to minimize the effect of dusting to provide clean and bright surfaces. This process is provided with the help of chemicals that prevent dust and form a bright film layer on the surface (anti-dust LUFTCHEM MIRROR 883)
All additive chemicals and catalysts are added directly to the resin before the impregnation (absorption) process. Once the drying process is complete, the impregnated papers can be kept in stock for a few months before being laminated onto the wooden panels. During hot pressing or thermo-melting, the resin in the paper softens sufficiently to form bonds with sub-layers. Later, the resin cures harden and turn into a form with high strength that protects the decor papers.
Separating chemicals (Release agent LUFTCHEM GOLD PLATE 520) provide a clean separation of laminated sheets from the press plate.
Printing speed and surface quality determine the correct choice of resin and resin catalyst / hardener.
All these additives and catalysts are added directly into the resin before the impregnation process.
Impregned paper are stocked by stacking on the pallet.
LUFTCHEM ANTI-BLOCK 777 (ANTIBLOCKING) has been used to prevent stacks of impregned paper in storage areas to adhesive and block with the effect of high temperature and high relative humidity.
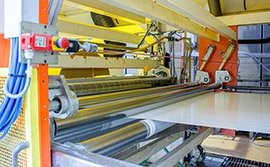
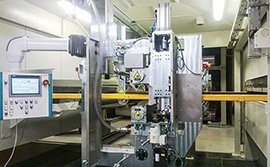
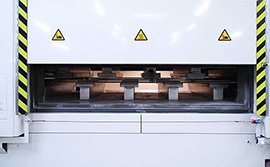
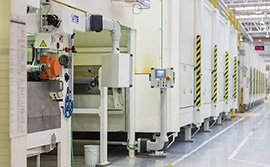
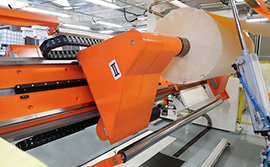
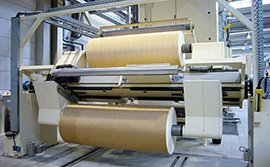
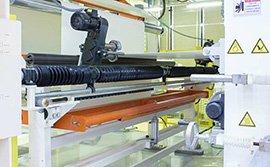
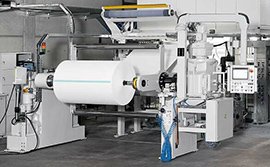